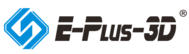
Eplus3D
About Us
Eplus3D was founded in 2014, the core technical team has more than 25 years of AM technology accumulation, has been engaged in research and development of industrial-grade Additive Manufacturing systems and application technologies, with MPBF™ (Metal Powder Bed Fusion) , PPBF™ (Polymer Powder Bed Fusion) and Stereo lithography 3D printing technology, provides professional application solutions for the fields of Aerospace, Automotive, Tooling, Health, Dental, Consumer Goods, Precision Manufacturing, etc.
Eplus3D has two facilities in Beijing and Hangzhou, with annual scientific research investment of more than 20% of the revenue with comprehensive invention patents, utility model patents, software copyrights, and appearance patents. It has made great achievements in the design, equipment, process, software, materials and post-processing for the additive manufacturing, with equipment has been exported to more than 40 countries and regions such as Europe, America, Japan, South Korea and Southeast Asia, etc.
Eplus 3D's core technical team has more than 25 years of AM technology accumulation, has been engaged in 3D printing equipment manufacturing and process research and development. Mr. Feng Tao, the founder of Eplus3D, presided over the development of China’s first Selective Laser Sintering (SLS) equipment in 1993, and cooperated with South China University of Technology, developed China’s first Selective Laser Melting (SLM) AM equipment in 2002.
Our values
After years of technology precipitation, Eplus3D has been at the forefront of its peers in the following six aspects:
Core technology of metal 3D printing
Laser scanning path planning, protective atmosphere control, rapid purification of two-stage filtration system, gas saving, efficient powder spreading, precise positioning of substrates, precise temperature control, manufacturing process process diagnosis and processing, etc.
High-performance metal component manufacturing process
Multi-laser optical path and power consistency, special design of wind field, mechanical performance fluctuation control and parameter matching, realize splicing accuracy and high quality performance.
Defect prediction and control of large-scale complex components
Research temperature field, velocity field, molten pool, analyze internal microstructure and metallurgical defect formation mechanism and control methods, establish a multi-scale prediction model of internal residual stress of components based on thermal-mechanical coupling, and develop control methods for deformation and cracking of components.
Process integration and optimization of "Material-Design-Performance"
Combining AM Technology--Generative Design--Simulation Analysis--Empirical Mechanical Performance, it`s realized high-quality manufacturing of high-performance complex metal parts, engineering plastic parts, and shock-absorbing elastic products.
Automation and intelligence of additive equipment
Based on quality control requirements and industry application scenarios, develop software and hardware supported by sensors, controllers, and intelligent algorithms to achieve smooth interaction, efficient processing, safety and reliability.
Material process development and delivery standard curing
Based on the principle of additive technology and equipment performance, develop appropriate material libraries, process parameters, and technical development routes, and provide users with mature material process parameter packages to quickly form reliable production capacity and achieve unified delivery standards.